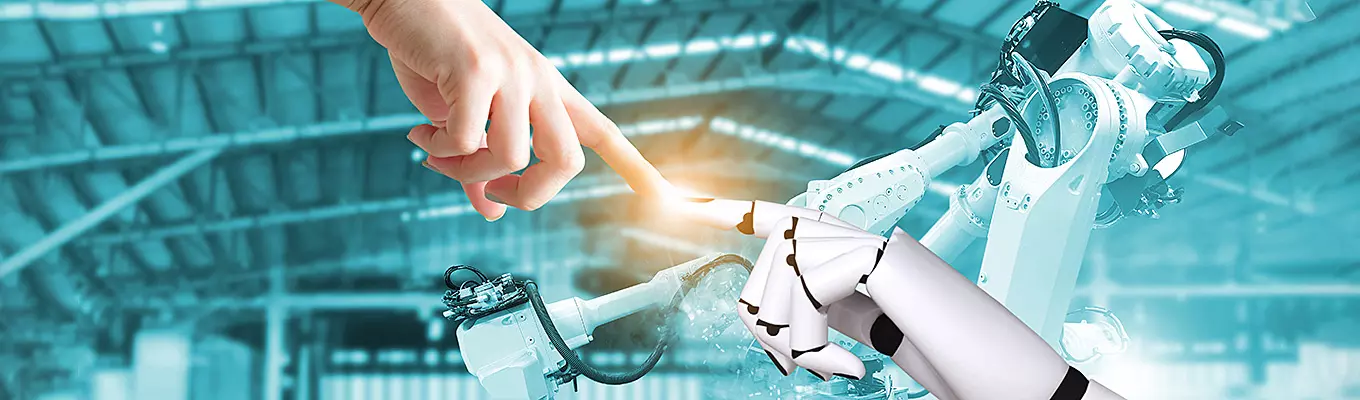
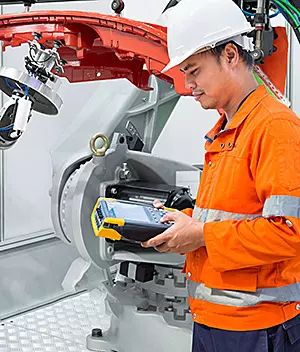
25. Mai 2023
Kollege Roboter - Arbeitssicherheit in der Mensch-Roboter-Kollaboration
Die direkte Zusammenarbeit von Mensch und Roboter ist keine utopische Vorstellung mehr, die uns nur in Science-Fiction-Filmen begegnet. Längst hat im Zuge von Industrie-4.0-Entwicklungen und Digitalisierungsprojekten die Mensch-Maschine- oder Mensch-Roboter-Kollaboration (MRK) Einzug in Fertigung und Service gehalten.
Der zentrale Unterschied zu althergebrachten, mit trennenden Schutzeinrichtungen versehenen Roboteranwendungen in der Industrie liegt also darin, dass bei MRK-Anwendungen Berührungen zwischen Maschine und Person im Bereich des Möglichen liegen und in einigen Fällen sogar erwünscht sind. Jedoch darf es auch in solchen Situationen selbstredend nicht zu Verletzungen des Nutzers, wie zum Beispiel Quetschungen oder Einklemmen, kommen.
Industrieroboter sind in der Fertigung meist starr vor Ort installiert, sie führen immer wieder die gleichen Arbeitsschritte aus und interagieren in der Regel nicht direkt mit Menschen. Um Berührungen und Zusammenstöße zu vermeiden, sind sie von Schutzzäunen oder Einhausungen umgeben. Industrieroboter, die ohne schützende Zäune direkt in einem Arbeitsraum zusammen mit Personen tätig sind, werden kollaborative Roboter genannt. Die Kurzbezeichnung lautet Cobot. Der Begriff setzt sich aus den englischen Worten „Collaboration“ und „Robot“ zusammen. So unterstützen Roboter beim Palettieren, Maschinenbeschicken, Montieren, Schrauben, Schweißen und Sortieren – fortwährend und in anhaltend hoher Qualität. Je enger diese Verknüpfung von Mensch und Maschine ausgeprägt ist, umso höher ist dann auch die Effizienz solcher Prozesse begründet in der Kombination menschlicher Stärken wie Geschicklichkeit, Kreativität und Urteilsvermögen mit den Vorteilen der Maschinen wie Kraft, Ausdauer und Wiederholgenauigkeit. So unterstützen und entlasten Roboter im gemeinsamen Arbeitsprozess den menschlichen Kollegen. Für zahlreiche Arbeitsplätze ergeben sich dadurch in weiteren Entwicklungsstufen neue Gestaltungsmöglichkeiten. Zunehmend sind kollaborierende Robotersysteme auch flexibel einsetzbar, was in Zeiten kleiner Losgrößen in der Fertigung von enormem wirtschaftlichem Vorteil sein kann.
Der zentrale Unterschied zu althergebrachten, mit trennenden Schutzeinrichtungen versehenen Roboteranwendungen in der Industrie liegt also darin, dass bei MRK-Anwendungen Berührungen zwischen Maschine und Person im Bereich des Möglichen liegen und in einigen Fällen sogar erwünscht sind. Jedoch darf es auch in solchen Situationen selbstredend nicht zu Verletzungen des Nutzers, wie zum Beispiel Quetschungen oder Einklemmen, kommen.
Was genau muss der Betreiber bzw. Arbeitgeber nun also beim Einsatz von Mensch-Roboter-Kollaboration unter Arbeitssicherheitsgesichtspunkten beachten?
Praktisch darf also kein Arbeitsmittel verwendet werden, solange nicht im Unternehmen eine entsprechende Gefährdungsbeurteilung vorliegt, aus der die Wahrscheinlichkeit bzw. die Risiken von Verletzungen ebenso hervorgehen wie entsprechende Präventionsmaßnahmen.
Da konstruktive Maßnahmen bei Entwicklung respektive Herstellung immer Vorrang vor den späteren Vorbeugemaßnahmen am Einsatzort des Roboters haben, stehen vor der Gefährdungsbeurteilung durch den Betreiber die EG-Konformitätserklärung und die Vergabe des CE-Zeichens durch den Hersteller bzw. Systemintegrator. Denn auch ein kollaborierender Roboter gilt als Maschine im Sinne der Maschinenrichtlinie.
Deshalb muss der Hersteller des Roboters bzw. der Systemintegrator, der die kollaborative Anwendung programmiert, testet und in das System des Betreibers implementiert, bereits im Fertigungsprozess und bei der Installation umfangreiche Risikobeurteilungen hinsichtlich eines Verletzungseintritts durchführen. Das gilt natürlich für das Gesamtsystem aus Kernroboter und die für seine Arbeitsaufgaben notwendigen Endeffektoren wie Greifer, Schrauber und Schweißköpfe.
An dieser Stelle ist zu beachten, dass der Betreiber schnell selbst zum Hersteller mit entsprechenden Pflichten zur Risikobeurteilung und Konformitätserklärung wird, wenn es im Betrieb zur Verknüpfung des Roboters mit weiteren Maschinen (oder Teilmaschinen) des kollaborierenden Arbeitssystems kommt, weil dabei unter Umständen durchaus eine neue, umfangreichere Maschine entsteht. Diese Problematik lässt sich eventuell an folgendem Beispiel näher erläutern: Eine große Videoanzeige wird aus vielen kleinen Standard-Videobildschirmen zusammengesetzt. Jeder dieser kleinen, konventionellen Bildschirme verfügt über eine entsprechende Konformitätserklärung, hier beispielsweise nach EMV-Richtlinie (elektromagnetische Verträglichkeit). Daraus darf jedoch keinesfalls abgeleitet werden, dass dann auch das große Videoarray automatisch dieser Richtlinie genügt, weshalb es als Gesamtkonstrukt nachträglich einer eigenständigen Bewertung unterzogen werden muss – so, als wenn es selbst das Endprodukt einer industriellen Geräteherstellung wäre.
Generell müssen also Risikobeurteilungen für kollaborierende Robotersysteme immer auf die Nähe von Person und Maschine eingehen sowie entsprechende Schutzmaßnahmen bei Kollisionen definieren. Mögliche Gefährdungen durch unbeabsichtigten Kontakt sind zu minimieren. Die aus der Risikobeurteilung folgenden Schutzmaßnahmen, die konstruktiv in die Maschine übernommen werden, können sich erstrecken von Lichtvorhängen über Begrenzung des Bewegungsbereiches des Roboters bis hin zu einer Kombination beider Maßnahmen.
Die Technische Spezifikation DIN ISO/TS 15066 (Roboter und Robotikgeräte – Kollaborierende Roboter) beschreibt Sicherheitsanforderungen an kollaborierende Industrierobotersysteme und deren Arbeitsumgebung. Sie stellt Schutzprinzipien für folgende Kollaborationsarten dar:
- Handführung
Hier wird der Roboterarm, der mit einem Werkzeug wie beispielsweise einem Greifer ausgestattet ist, aktiv vom Bediener gesteuert. Unter Arbeitssicherheitsgesichtspunkten muss der Roboter mit sicher reduzierter Geschwindigkeit arbeiten, die im Rahmen der Risikobeurteilung festgelegt wird. - Sicherheitsgerichteter, überwachter Stillstand
Kameras und optische Sensoren berechnen Schutzzonen und überwachen die räumlich nicht getrennten Arbeitsbereiche zwischen Mensch und Roboter. Wenn eine Person in den gemeinsamen Arbeitsbereich eintritt, stoppt der Roboter seine Tätigkeit, bis die Person den Arbeitsbereich wieder verlässt. Kollisionen werden ausgeschlossen, da der Roboter im Stillstand ist, wenn sich ein Mensch in seinem Arbeitsbereich aufhält. - Geschwindigkeits- und Abstandsüberwachung
Der Mensch hat während der Arbeit Zugang zum gemeinsamen Arbeitsraum. Unerwünschter Kontakt wird durch den Abstand zwischen den Protagonisten verhindert. Der Roboter erkennt, wenn der sicherheitsrelevante Abstand unterschritten wird, und stoppt in dieser Situation seine Arbeit. - Leistungs- und Kraftmessung
Mensch und Roboter arbeiten gleichzeitig in einem Arbeitsbereich. Kontakt zwischen ihnen ist möglich und im Einzelfall auch erwünscht. Die Sicherheit ist gewährleistet, da die roboterseitigen Kräfte reduziert sind und die Verletzungsgefahr für die Person bei Kontakt sehr reduziert ist. Verletzungen sind weitgehend ausgeschlossen, wenn der Roboter über runde, gepolsterte Kanten oder Ähnliches verfügt.
Die DIN ISO/TS 15066 kann bei der Risikobeurteilung ebenso herangezogen werden wie Teil 1 und 2 der DIN EN ISO 10218 (Industrieroboter – Sicherheitsanforderungen), die die Anforderungen der Maschinenrichtlinie für die spezielle Anwendungsart konkretisieren. Technische Merkmale, die im Rahmen der Risikobeurteilung zur Minimierung der Verletzungsgefahr durch Kontakt betrachtet werden, sind zum Beispiel:
- Der Roboter muss mit intelligenten, dynamischen Sensoren sowie zuverlässigen Steuerungen ausgestattet sein, um unerwünschten Kontakt zu vermeiden.
- Die eingesetzten Roboterwerkzeuge (Greifer usw.) sollen ohne scharfe und spitze Kanten bzw. ohne Scherkanten ausgeführt oder gepolstert sein, um das Verletzungsrisiko bei unerwünschtem Kontakt zu minimieren.
- Biomechanische Grenzwerte (Druck und Kraft, die vom Roboter ausgehen) müssen für Kontaktszenarien definiert werden, um mit ihrer Hilfe die Verletzungsschwere bei ungewollten Kollisionen und die entsprechende Toleranzschwelle bewerten zu können.
Gefährdungen, die sich konstruktiv nicht ausräumen lassen und somit auch nicht durch Schutzeinrichtungen beseitigt werden können, sind als Restrisiken in der technischen Dokumentation festzuhalten.
Unabhängig von der vorab beschriebenen Risikobeurteilung des Herstellers ist der Betreiber verpflichtet, eine Gefährdungsbeurteilung (GBU) für die MRK-Anwendung am speziell vorgesehenen Arbeitsplatz durchzuführen. Eine GBU, die auf die Risiken bei der Nutzung einer MRK-Anwendung eingeht und entsprechende Präventionsmaßnahmen definiert, ist deshalb für den betreibenden Arbeitgeber unumgänglich. Um eine solche rechtssichere GBU erstellen zu können, sind umfangreiche Kenntnisse des Gefährdungspotenzials des bewerteten Arbeitsmittels notwendig.
Die GBU geht ein auf mögliche Gefährdungen am Arbeitsplatz unter Einsatz der MRK-Anwendung, Risiken für den Eintritt von Gefährdungen und entsprechend notwendige Schutzmaßnahmen, um das Gefährdungsszenario praktisch zu verhindern. Grundlegend sind daher die mechanischen Gefährdungen für verschiedene Nutzergruppen wie Bediener, Programmierer oder auch Besucher aufgrund von Kollision mit dem Roboter zu beurteilen. Hinzu kommen elektrische Gefährdungen und ergonomische Gesichtspunkte. Notwendiges Faktenwissen zur Anfertigung der Gefährdungsbeurteilung findet der Betreiber in der Betriebsanleitung, die ihm vom Hersteller bzw. Systemintegrator neben der EG-Konformitätserklärung und speziellen Zusatzinformationen zu biomechanischen Grenzwerten bei Kollisionen zur Verfügung gestellt werden muss. Ergänzend zu diesen Materialien sollte der Betreiber außerdem die Risikobeurteilung und technische Dokumentation als unterstützende Unterlagen beim Hersteller/Systemintegrator anfordern.
Aber auch psychische Aspekte sollten in der GBU für Arbeitsplätze mit kollaborierenden Robotern betrachtet werden. Die direkte Arbeit mit einem Roboter ist nicht für jeden Mitarbeiter akzeptabel. Trotz objektiv vorhandener technischer Schutzeinrichtungen und Sicherheitssteuerungen kann sich gelegentlich die gefühlte Sicherheit jeweils betroffener Personen in puncto Verletzungsrisiko durch den Roboter deutlich unterscheiden. Ein weiterer psychischer Aspekt, der beim Einsatz von MRK-Anwendungen übergeordnet eine Rolle spielt, ist die Frage von Ängsten vor Verlust des Arbeitsplatzes oder der Umgang mit einer kommunikationsarmen technisierten Arbeitsumgebung.
Neben der arbeitsplatzspezifischen GBU sind natürlich spezielle Betriebsanweisungen und Informationen des Betreibers an den Benutzer notwendig, um Unfälle zu vermeiden. Auch diese Mitteilungen sind übrigens als Schutzmaßnahmen im Sinne der Gefährdungsbeurteilung zu sehen, denn die Benutzer müssen gezielt in die Lage versetzt werden, die MRK-Anwendung gefahrfrei nutzen zu können. Eine wichtige Quelle für den Betreiber ist auch hier die Betriebsanleitung des MRK-Systems, die er bei Auslieferung erhalten muss. In der Betriebsanleitung müssen die Maßnahmen erläutert sein, die vom Betreiber zum Schutz der Nutzer an diese zu kommunizieren sind. Beispielhaft seien hierzu Anweisungen zum Verhalten bei Störungen oder Notfällen bzw. dem ausschließlichen Einsatz von entsprechend qualifiziertem und unterwiesenem Personal angeführt.
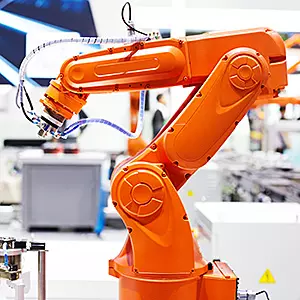
Welche Einsatzmöglichkeiten und Kollaborationsarten gibt es?
Zusammenfassung und Fazit
Bleiben Sie wissbegierig!
(Der Artikel wurde zuerst auf www.praevention-aktuell.de veröffentlicht.)
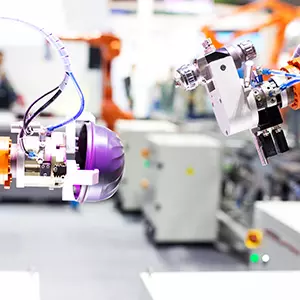
Zugehörige Produkte
Arbeitsschutzmanagementbeauftragter (TÜV®) nach DIN EN ISO 45001
Freie Plätze : 100
Präsenz
|
Live-Webinar