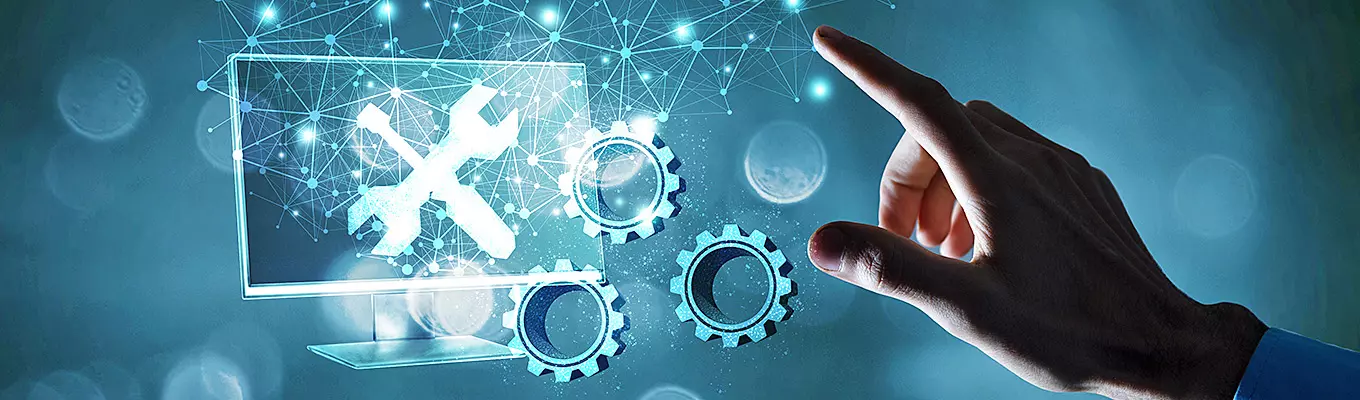
Ein Vorteil der vorausschauenden Instandhaltung ist, dass dank der Kenntnisse, wann für welche Anlagen oder Geräte eine Wartung ansteht, die Kapazitäts- und Ressourcenplanung durch die Instandhaltungsabteilung effizienter gestaltbar wird. Es ist klarer, welche Ersatz-/Austauschteile bzw. Personalstärken zu welchem Zeitpunkt verfügbar sein müssen.
Zugehörige Produkte